Accurate & Easy Linehaul Tracking in Australia – Stay Updated Always
Our user-friendly linehaul tracking Australia tools let you monitor your cargo in real time, giving you full visibility and peace of mind.
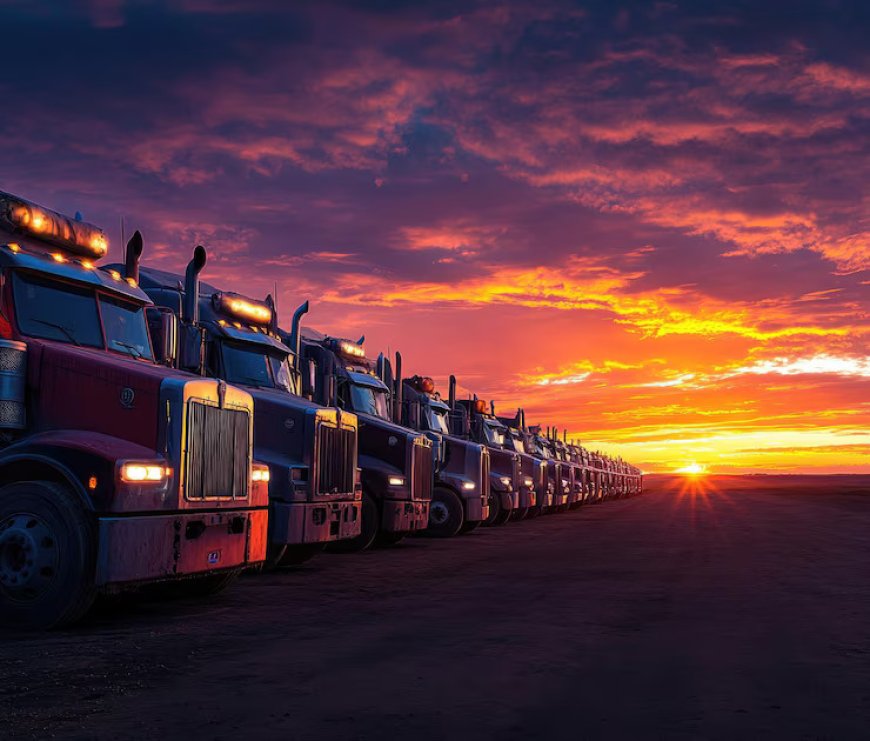
Picture this: You're a warehouse manager in Melbourne, and you've got a shipment of critical automotive parts heading to Perth. It's Thursday afternoon, and your client is breathing down your neck about delivery timelines. Sound familiar? If you've ever found yourself constantly refreshing tracking pages or making countless phone calls to freight companies, you're not alone. The good news is that linehaul tracking Australia has evolved dramatically, and staying on top of your freight movements doesn't have to be a source of stress anymore.
Why Linehaul Tracking Matters More Than Ever
The Australian logistics landscape is unique, and frankly, it's challenging. We're talking about a continent where your freight might travel from Sydney to Darwin – a distance that's roughly equivalent to shipping from London to Morocco. When you factor in weather delays, road conditions, and the sheer scale of operations, knowing exactly where your goods are becomes absolutely crucial.
I remember chatting with a logistics coordinator last year who told me about a nightmare scenario where a shipment of pharmaceuticals went missing for three days. Not misplaced – just completely off the radar. The financial impact was substantial, but the stress and reputation damage were even worse. This kind of situation is exactly why accurate tracking has become non-negotiable in today's business environment.
The Real-World Impact of Poor Tracking
Let's be honest about what happens when tracking systems fail. It's not just about delayed deliveries. Poor visibility creates a domino effect that ripples through your entire supply chain. Your customers lose confidence, your planning becomes reactive rather than proactive, and your team spends more time firefighting than actually growing the business.
Consider the mining industry in Western Australia. When equipment parts are en route to remote sites, every hour of delay can cost thousands in lost productivity. Without reliable tracking, site managers can't make informed decisions about whether to source alternative parts or adjust their operational schedules. The uncertainty alone can grind operations to a halt.
What Makes Tracking Systems Actually Work
The difference between a good tracking system and a great one often comes down to data quality and frequency of updates. The best systems don't just tell you that your freight left Adelaide yesterday – they provide real-time updates about road conditions, estimated arrival times, and any potential disruptions along the route.
Real-time GPS tracking has revolutionized how we monitor linehaul movements. Instead of relying on manual check-ins at depots, modern systems provide continuous location data. This means you can see exactly where your freight is at any given moment, not just when it reaches predetermined checkpoints.
Temperature monitoring has also become increasingly important, especially for sensitive goods. Imagine shipping fresh produce from Queensland to Tasmania. You need to know not just where your goods are, but also whether they're maintaining the right temperature throughout the journey. Integrated tracking systems now provide this level of detail as standard.
The Technology Behind Seamless Tracking
Modern tracking systems leverage a combination of GPS, cellular networks, and sophisticated algorithms to provide accurate, real-time updates. The integration of IoT sensors means that tracking extends beyond simple location data to include information about cargo condition, security, and even driving behavior.
Machine learning algorithms analyze historical data to predict potential delays and suggest alternative routes. This proactive approach means you're not just reacting to problems – you're preventing them. Companies like Big Wheels Transport have invested heavily in these advanced systems, understanding that predictive analytics can be the difference between satisfied customers and lost business.
Making Tracking Work for Your Business
The key to effective tracking isn't just having the technology – it's knowing how to use it strategically. Smart businesses set up automated alerts for critical shipments, establish clear escalation procedures when delays occur, and use tracking data to optimize their logistics planning.
Consider setting up geofenced alerts for important deliveries. When your freight enters specific zones – perhaps when it's 50 kilometers from the destination – you can automatically notify relevant stakeholders. This simple automation can significantly improve customer satisfaction and reduce the workload on your operations team.
Integration with Existing Systems
The most effective tracking solutions integrate seamlessly with your existing business systems. Your tracking data should flow directly into your inventory management system, your customer relationship management platform, and your financial systems. This integration eliminates manual data entry and reduces the risk of errors.
API connectivity has made this integration much more straightforward than it used to be. Modern tracking platforms can push data directly to your systems, ensuring that everyone in your organization has access to the same real-time information.
The Future of Linehaul Tracking
Looking ahead, tracking systems are becoming increasingly sophisticated. Artificial intelligence is being used to predict delivery times with remarkable accuracy, taking into account factors like weather patterns, traffic conditions, and historical performance data.
Blockchain technology is also making inroads into freight tracking, providing an immutable record of a shipment's journey. This is particularly valuable for high-value goods or shipments requiring compliance documentation.
Best Practices for Implementation
When implementing a new tracking system, start with your most critical shipments. Don't try to track everything at once – focus on the freight that has the biggest impact on your business. This targeted approach allows you to refine your processes before rolling out tracking more broadly.
Training your team is crucial. The best tracking system in the world won't help if your staff doesn't know how to use it effectively. Invest time in proper training and establish clear procedures for responding to tracking alerts.
Measuring Success
The success of your tracking implementation should be measured not just in terms of system uptime or data accuracy, but in business outcomes. Are your customers reporting higher satisfaction levels? Are you experiencing fewer emergency situations? Is your team spending less time on reactive problem-solving?
Regular review of your tracking data can also reveal optimization opportunities. Perhaps certain routes consistently experience delays, or maybe specific carriers perform better than others. This intelligence can inform strategic decisions about your logistics network.
Conclusion
Effective linehaul tracking in Australia isn't just about knowing where your freight is – it's about having the information you need to make smart business decisions. The investment in proper tracking systems pays dividends in customer satisfaction, operational efficiency, and peace of mind.
The logistics landscape will continue to evolve, but the fundamental need for accurate, real-time information about your freight movements isn't going anywhere. By implementing robust tracking systems and using the data strategically, you can transform logistics from a source of stress into a competitive advantage.
Remember, the goal isn't perfect tracking – it's actionable intelligence that helps your business run more smoothly. When you have that level of visibility into your supply chain, you're not just staying updated – you're staying ahead.